Products ordered and identified as KEEP FROM FREEZING should not be shipped during periods where temperatures will reach below zero.
Customer accepts full responsibility for the risk of freezing during transit on orders placed during colder weather conditions.
New Products
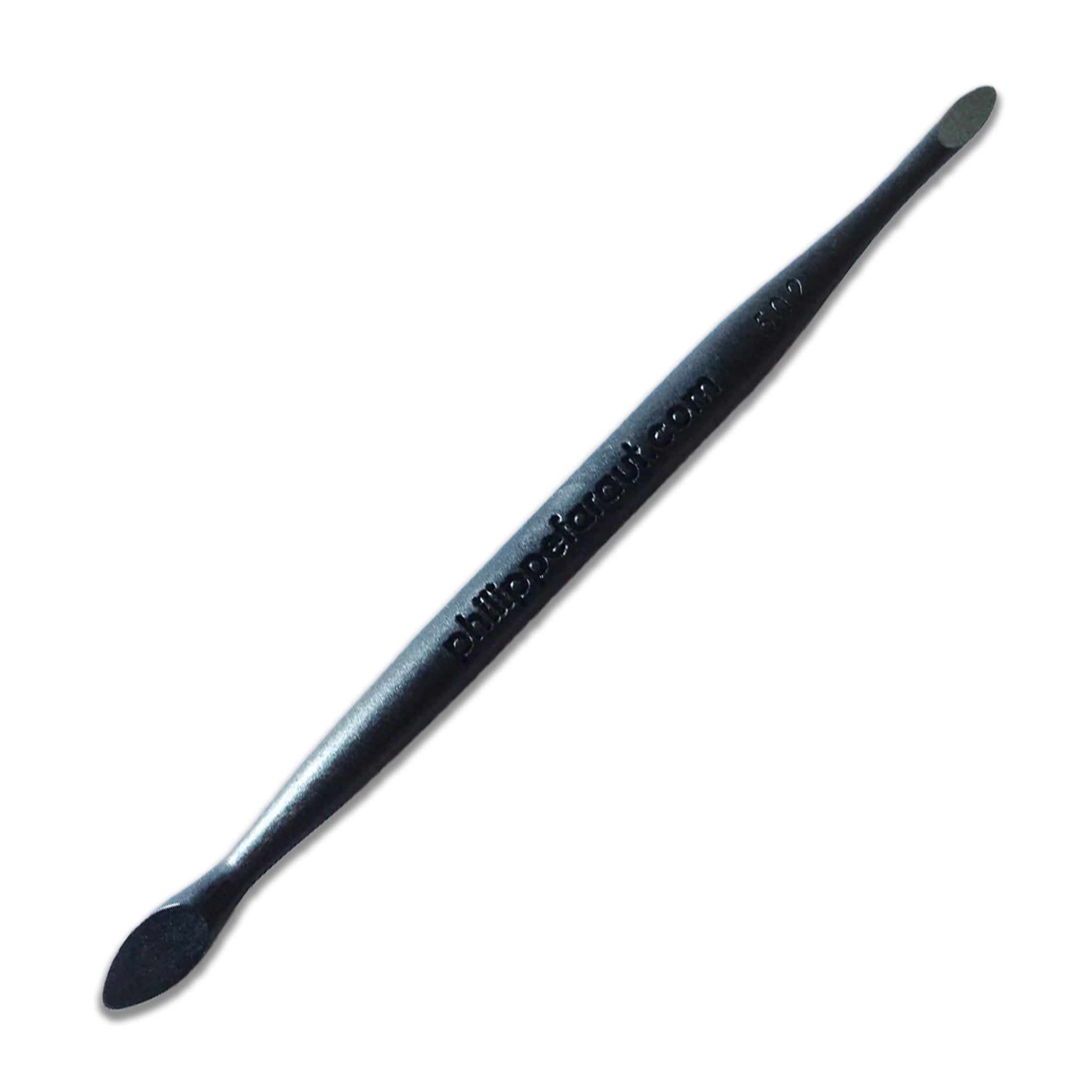
Clay Modeling Eye Tool 7in
Sale price$15.99
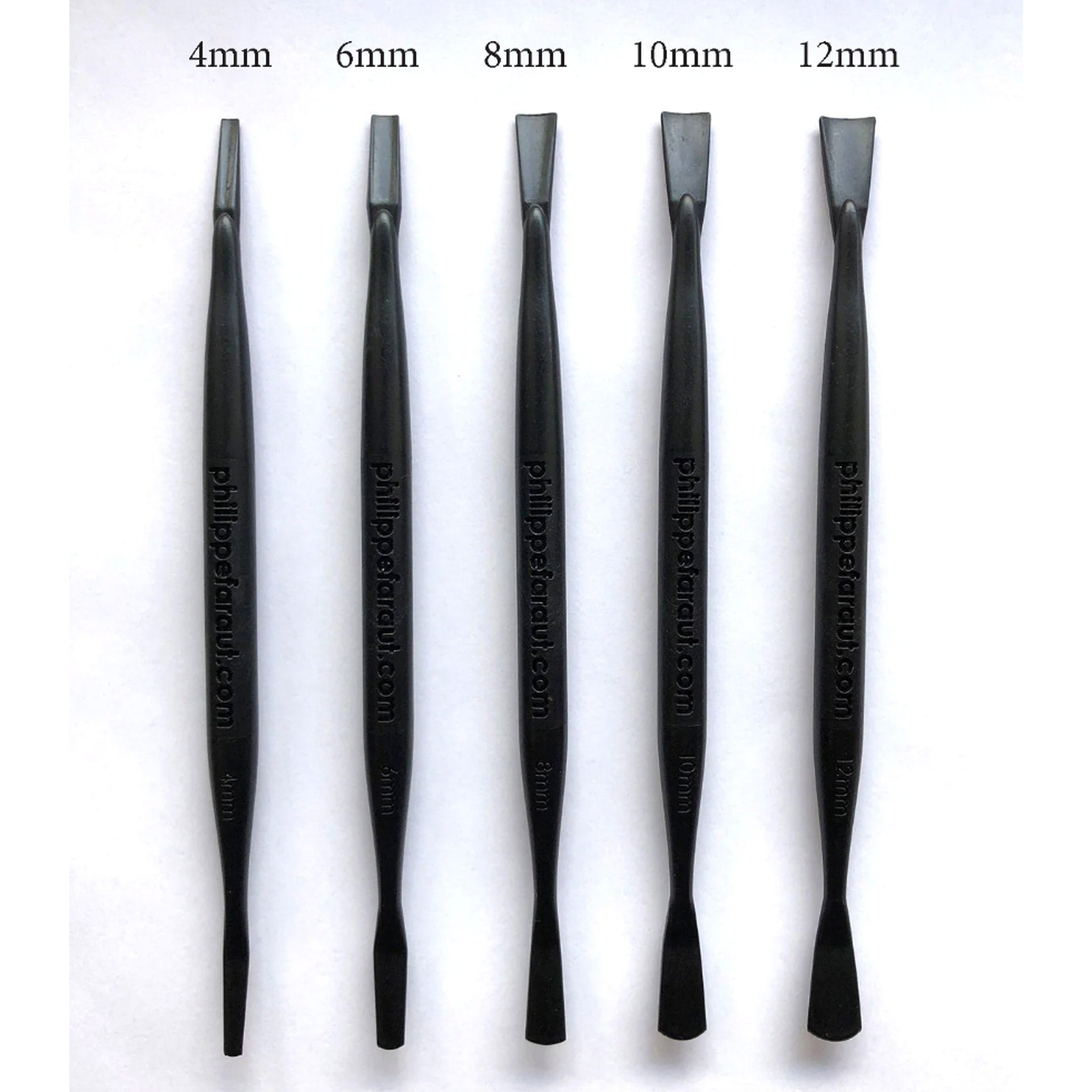
Finger Tools Set
Sale price$59.98
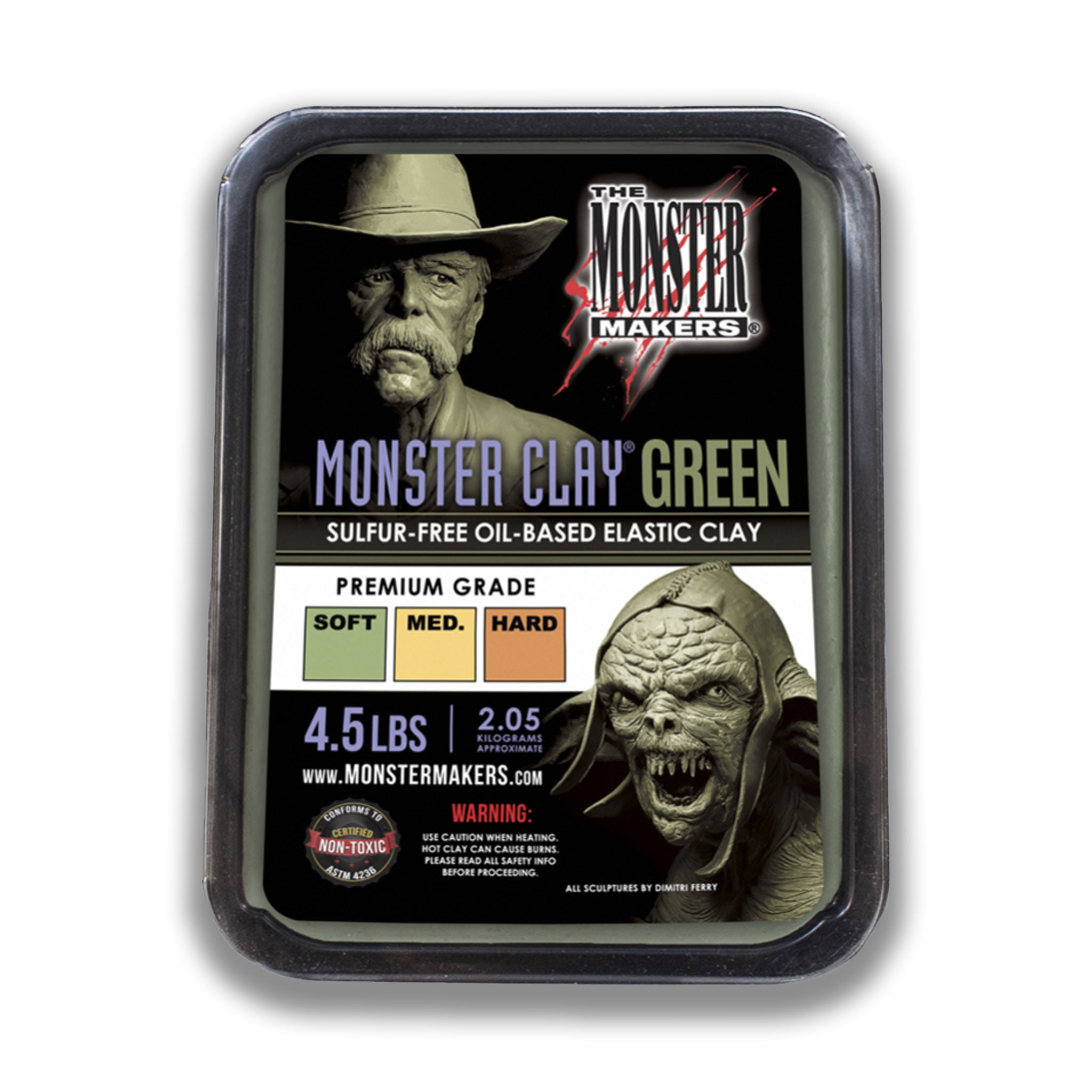
Monster Makers Premium Clay GREEN
Sale price$37.20
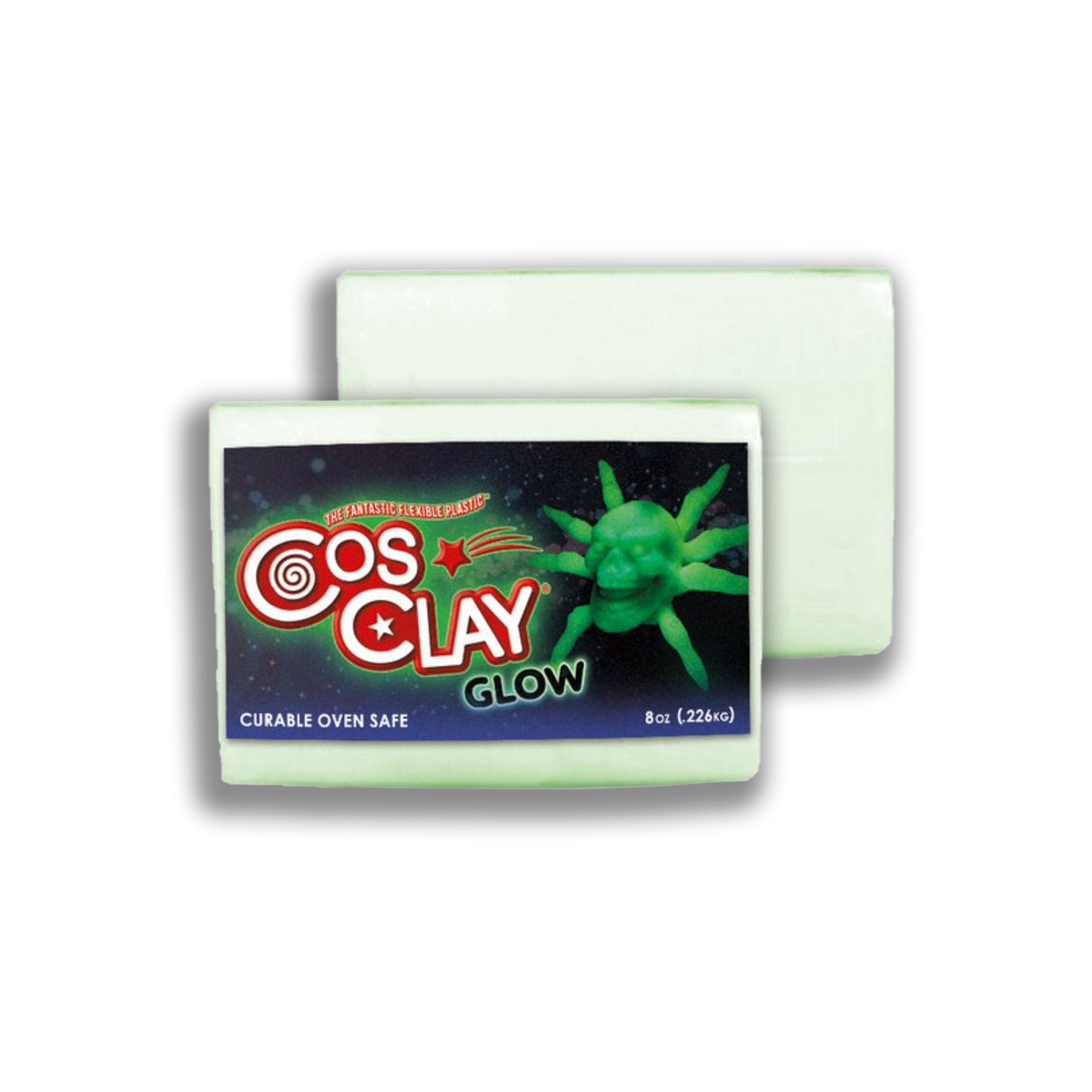
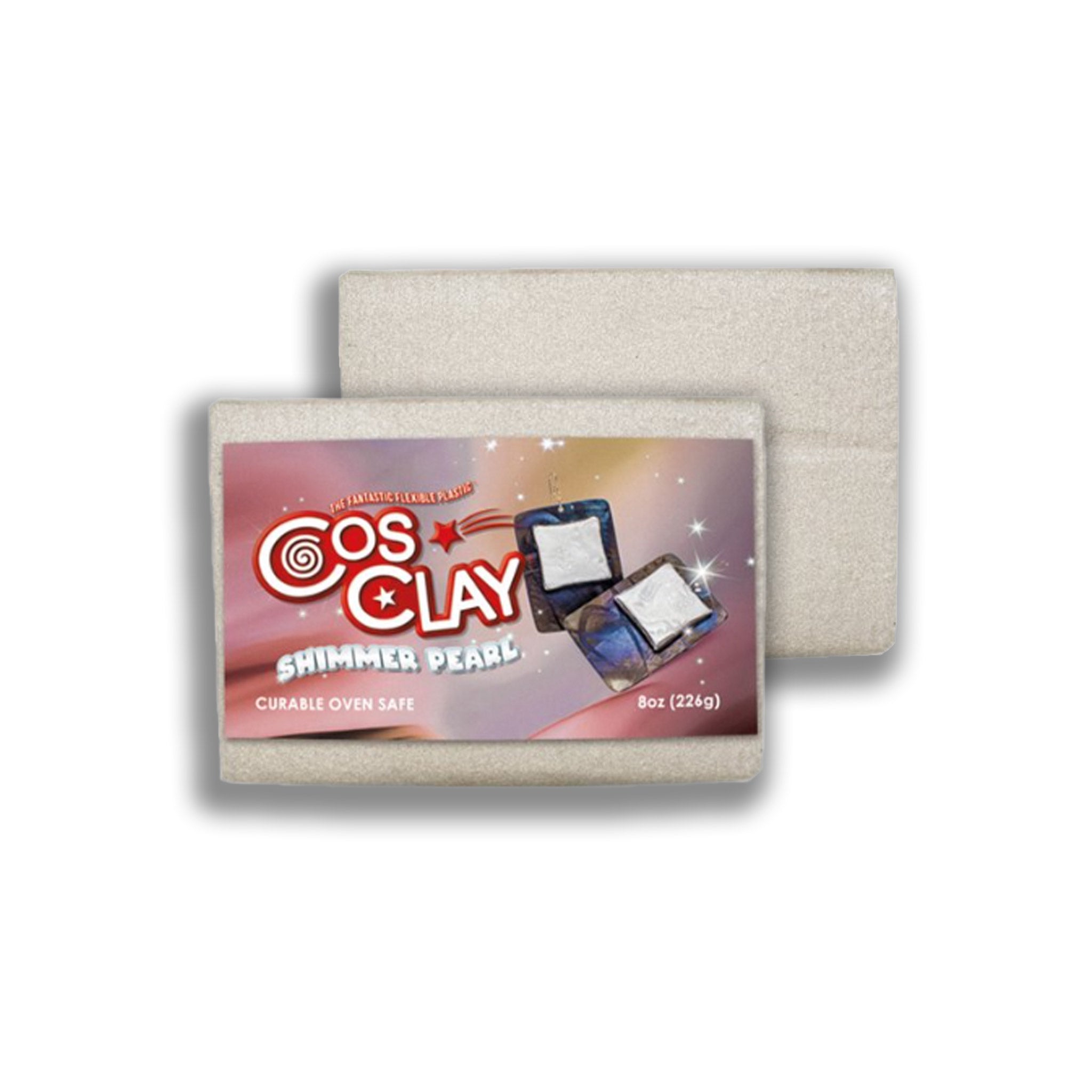
Cosclay Elements
Sale priceFrom $17.43
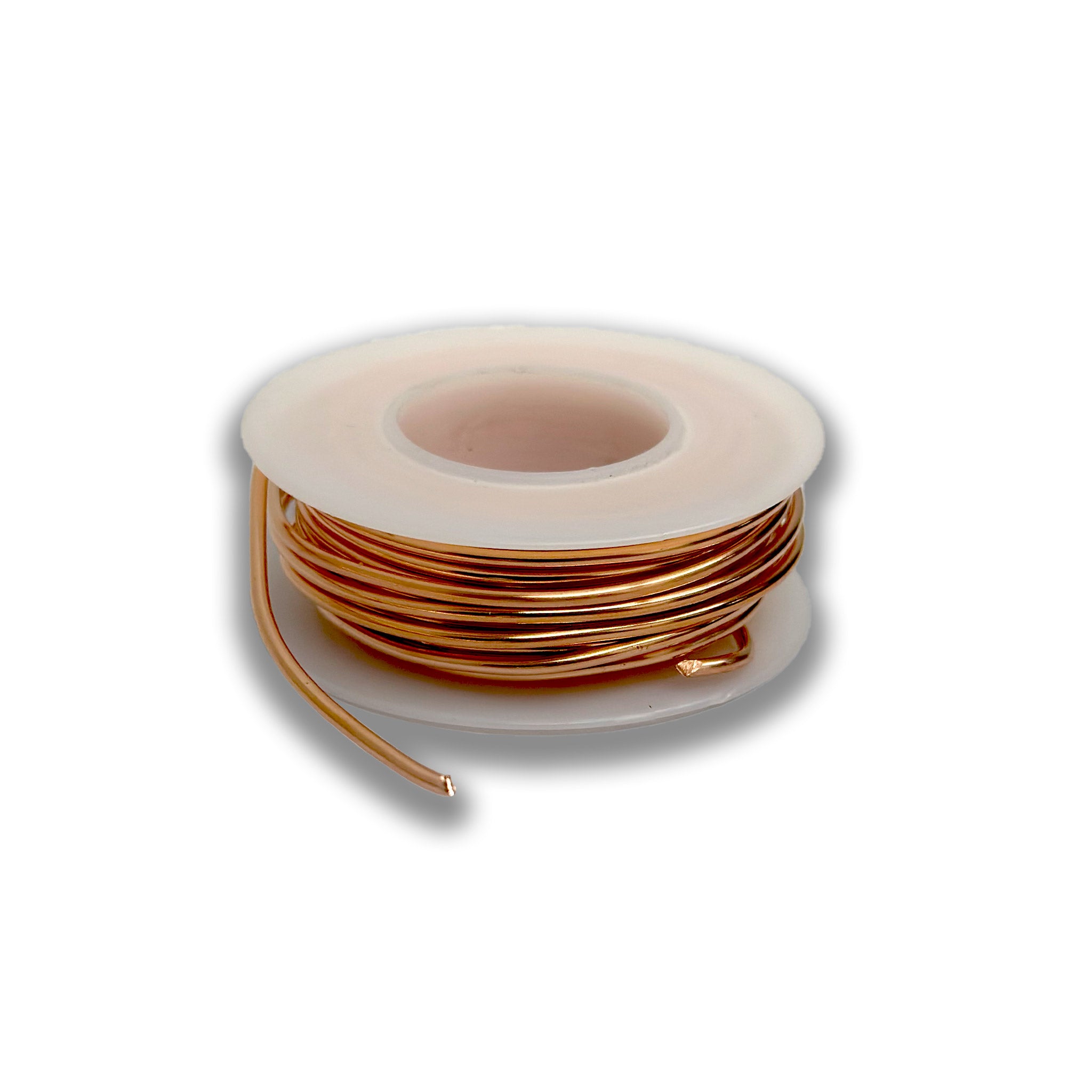
Copper Wire 1/16 in (0.064)
Sale price$14.99
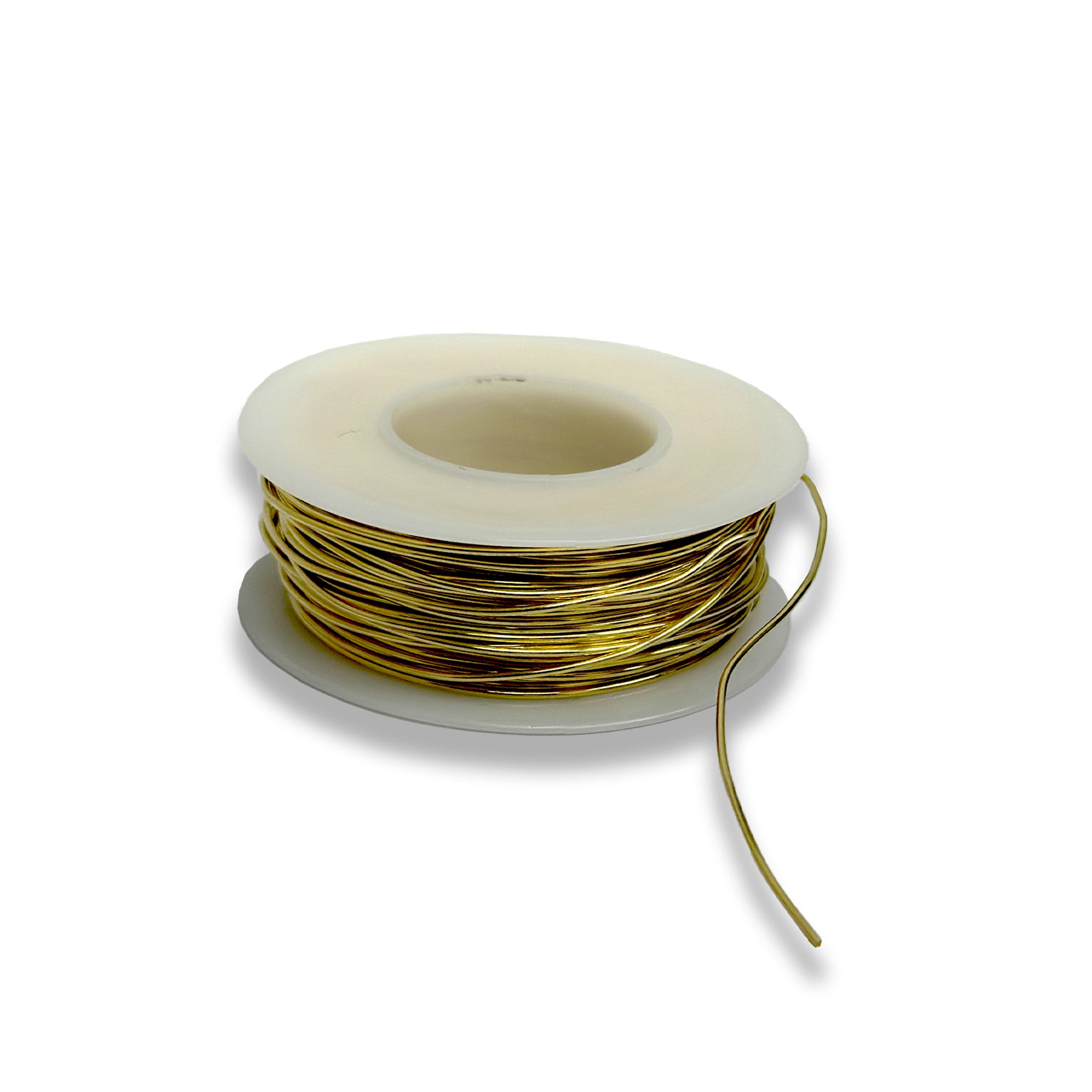
Yellow Brass Wire 1/32 in (.032)
Sale price$18.99